Sommaire
Dans un monde où la technologie redessine continuellement le paysage industriel, la révolution numérique s'impose comme un vecteur de transformation majeur pour les pratiques ergonomiques en usine. L'intégration croissante de solutions numériques ouvre la voie à des environnements de travail optimisés, à la fois pour la productivité et le bien-être des opérateurs. Cet article explore comment les avancées technologiques façonnent les méthodes de travail et révolutionnent l'ergonomie sur les chaînes de production. Des outils intelligents aux systèmes automatisés, découvrez les multiples facettes de cette métamorphose industrielle. Laissez-vous guider à travers les couloirs de l'usine moderne, où chaque aspect de la production est repensé sous le prisme du numérique. Embarquez pour un voyage au cœur des changements qui redéfinissent l'espace de travail industriel et préparez-vous à envisager l'ergonomie sous un jour entièrement nouveau. L'heure est à la découverte des pratiques qui dessinent l'avenir des usines, un avenir où l'humain et la technologie avancent main dans la main.
Les nouveaux outils de l'ergonomie numérique
Dans le contexte des usines modernes, l'ergonomie numérique se positionne au cœur de l'innovation, avec des solutions avancées pour garantir le bien-être et l'efficacité des travailleurs. Parmi ces avancées, les exosquelettes assistés par ordinateur se distinguent comme des dispositifs de soutien musculo-squelettique, réduisant la fatigue et les risques de blessures liés à des tâches répétitives ou de manutention lourde. En parallèle, des interfaces utilisateur de plus en plus intuitives facilitent l'interaction homme-machine, permettant une prise en main rapide et une réduction des erreurs opérationnelles. Les capteurs de mouvement, quant à eux, jouent un rôle prépondérant dans l'analyse biomécanique, offrant aux spécialistes en ergonomie industrielle des données précises pour optimiser les postures et les gestes des opérateurs sur les chaînes de production. Ces technologies convergent vers une amélioration tangible de l'environnement de travail au sein des usines modernes, marquant une avancée significative dans la protection et le confort des travailleurs.
L'impact de la big data sur l'ergonomie
L'avènement de la big data dans l'industrie a marqué un tournant décisif dans l'amélioration des conditions de travail. Grâce à la collecte et à l'analyse de données massives, les data analysts spécialisés en ergonomie milieu industriel peuvent désormais concevoir des environnements de travail qui s'adaptent aux besoins spécifiques de chaque employé. Cela se manifeste par la personnalisation des postes de travail, où les aspects de l'ergonomie cognitive sont pris en compte pour réduire la fatigue mentale et optimiser les processus de décision.
La big data permet également une amélioration continue de l'ergonomie, car les données récoltées sont constamment analysées pour déceler les domaines nécessitant des ajustements. Ainsi, les risques de blessures sont minimisés, et les performances augmentent grâce à une meilleure adéquation entre l'opérateur et son poste de travail. L'intégration de la big data dans les stratégies ergonomiques représente par conséquent une avancée significative pour garantir des conditions de travail optimales et soutenir la santé des salariés dans l'industrie.
La réalité virtuelle et augmentée au service de la formation
L'intégration de la réalité virtuelle (RV) et de la réalité augmentée (RA) dans les processus de formation en milieu industriel marque une étape décisive dans l'évolution des méthodes pédagogiques. Ces technologies immersives proposent une simulation d'environnement de travail qui révolutionne l'acquisition des compétences, notamment en matière de formation ergonomique. En plaçant les employés au cœur de scénarios virtuels, la RV et la RA facilitent l'apprentissage de gestes précis et sûrs, minimisant ainsi les risques d'accidents et les troubles musculosquelettiques souvent associés aux postures inappropriées.
Ce type de formation, élaboré par des spécialistes en formation industrielle, utilise des programmes sophistiqués pour reproduire les conditions réelles d'une chaîne de production. Par le biais de ces environnements simulés, les employés peuvent répéter les mouvements et les tâches de manière intensive sans les contraintes ou les dangers d'un environnement de production actif. L'immersion dans des scénarios réalistes améliore non seulement leur compréhension des enjeux ergonomiques mais aussi leur réactivité face à des situations potentiellement dangereuses.
La prévention des accidents devient ainsi plus interactive et efficace. Les travailleurs sont mieux préparés à identifier et à réagir aux risques, ce qui engendre une baisse significative des incidents et contribue à une culture de sécurité renforcée au sein de l'entreprise. De surcroît, la formation par RV et RA favorise une mémorisation à long terme des bonnes pratiques ergonomiques, un atout non négligeable pour la santé et la productivité des salariés.
En conclusion, la réalité virtuelle et la réalité augmentée s'imposent comme des leviers de transformation dans le domaine de la formation industrielle. Elles offrent des solutions innovantes pour l'apprentissage des gestes ergonomiques et jouent un rôle prépondérant dans la prévention des accidents, témoignant ainsi de l'impact profond de la révolution numérique sur les pratiques ergonomiques dans les usines modernes.
Automatisation et robotique : partenaires de l'ergonomie
L'automatisation et la robotique, notamment à travers l'introduction des robots collaboratifs ou cobots, jouent un rôle déterminant dans l'amélioration des conditions de travail au sein des usines modernes. En prenant en charge les tâches physiques ardues et monotones, ces technologies réduisent considérablement les risques de troubles musculo-squelettiques et autres blessures liées à l'effort répétitif. L'ergonomie en usine est ainsi grandement optimisée, favorisant un environnement de travail plus sain et productif. De surcroît, l'implémentation d'une interface homme-machine bien conçue garantit une interaction intuitive et sécuritaire entre l'opérateur humain et les machines automatisées, élément prépondérant pour la sécurité et l'efficacité des processus industriels.
Les défis et opportunités de l'intégration numérique
L'intégration des technologies digitales au sein des usines présente des défis non négligeables, dont la formation du personnel se dresse en première ligne. Les systèmes cyber-physiques, pierres angulaires de cette transformation, requièrent des compétences spécifiques, complexifiant le parcours de formation des opérateurs. Les coûts d'investissement constituent également un enjeu majeur, impliquant des décisions stratégiques quant à l'allocation des ressources financières. Néanmoins, cette évolution numérique offre des opportunités considérables. Elle contribue à rehausser l'attractivité des emplois industriels, souvent perçus comme dépassés, en les dynamisant grâce à l'innovation technologique. De surcroît, l'amélioration de la qualité de vie au travail émerge comme un avantage indéniable, grâce à des environnements de travail plus sécurisés et ergonomiques, conçus pour réduire la fatigue et accroître l'efficience des employés.
Sur le même sujet
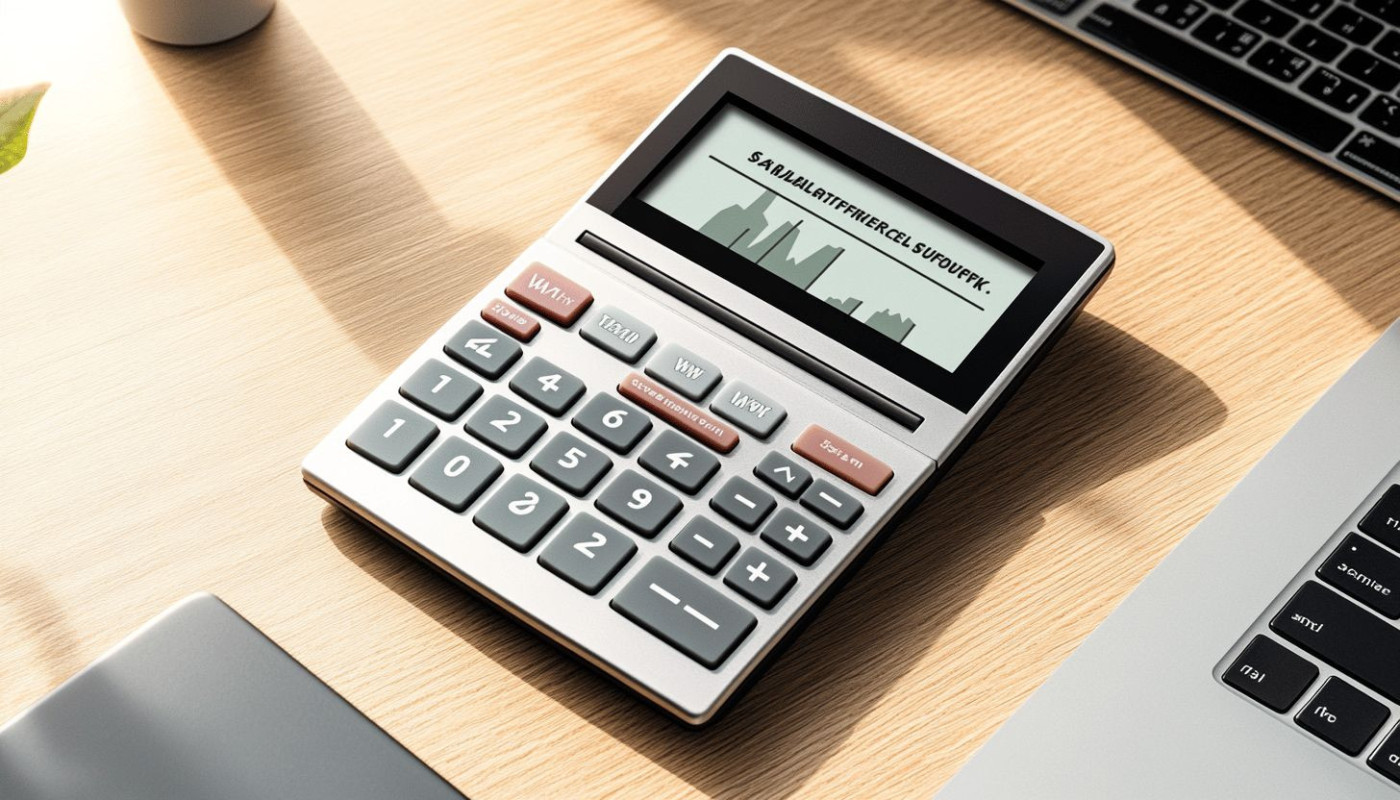
Comment estimer son salaire net en portage salarial à l'aide d'un simulateur
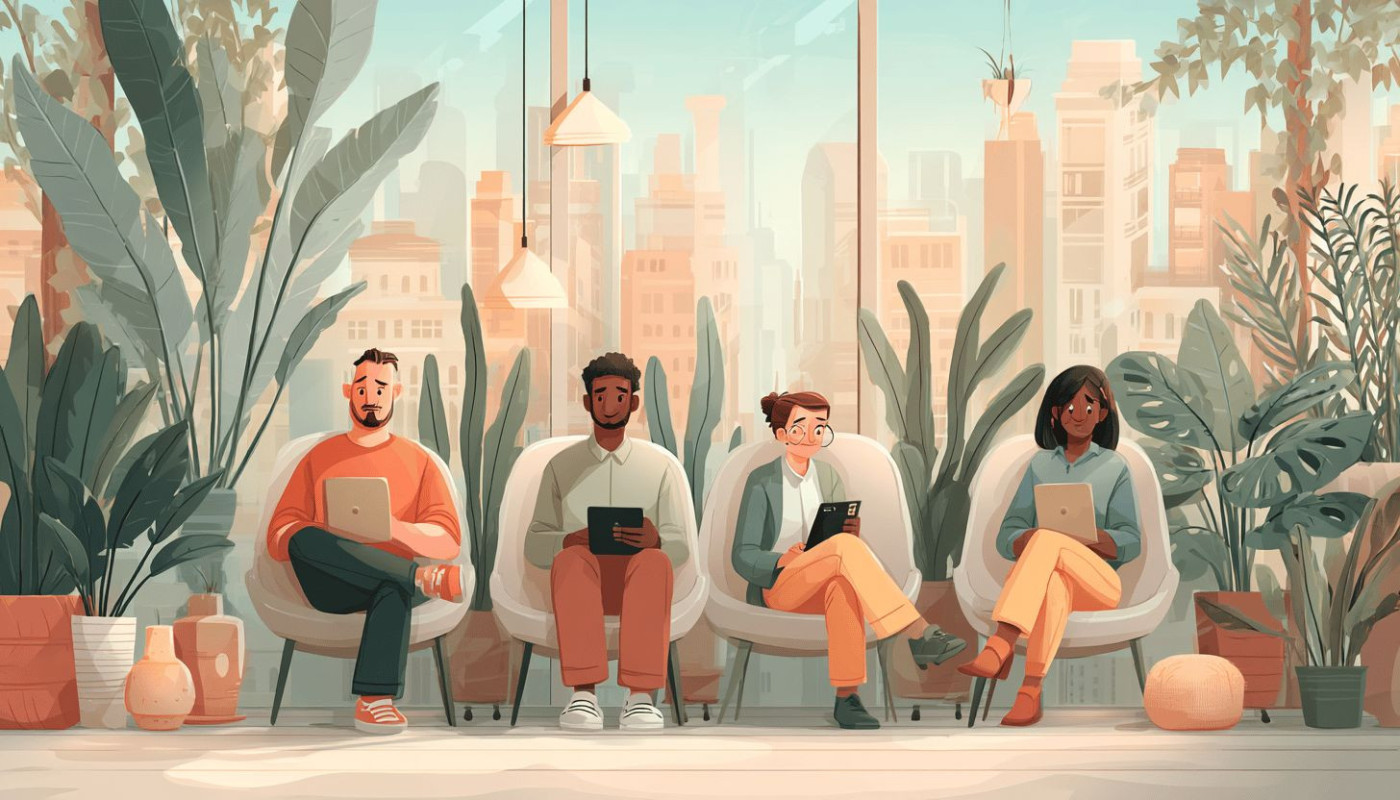
Gestion des talents à l'ère numérique outils et stratégies pour une équipe performante
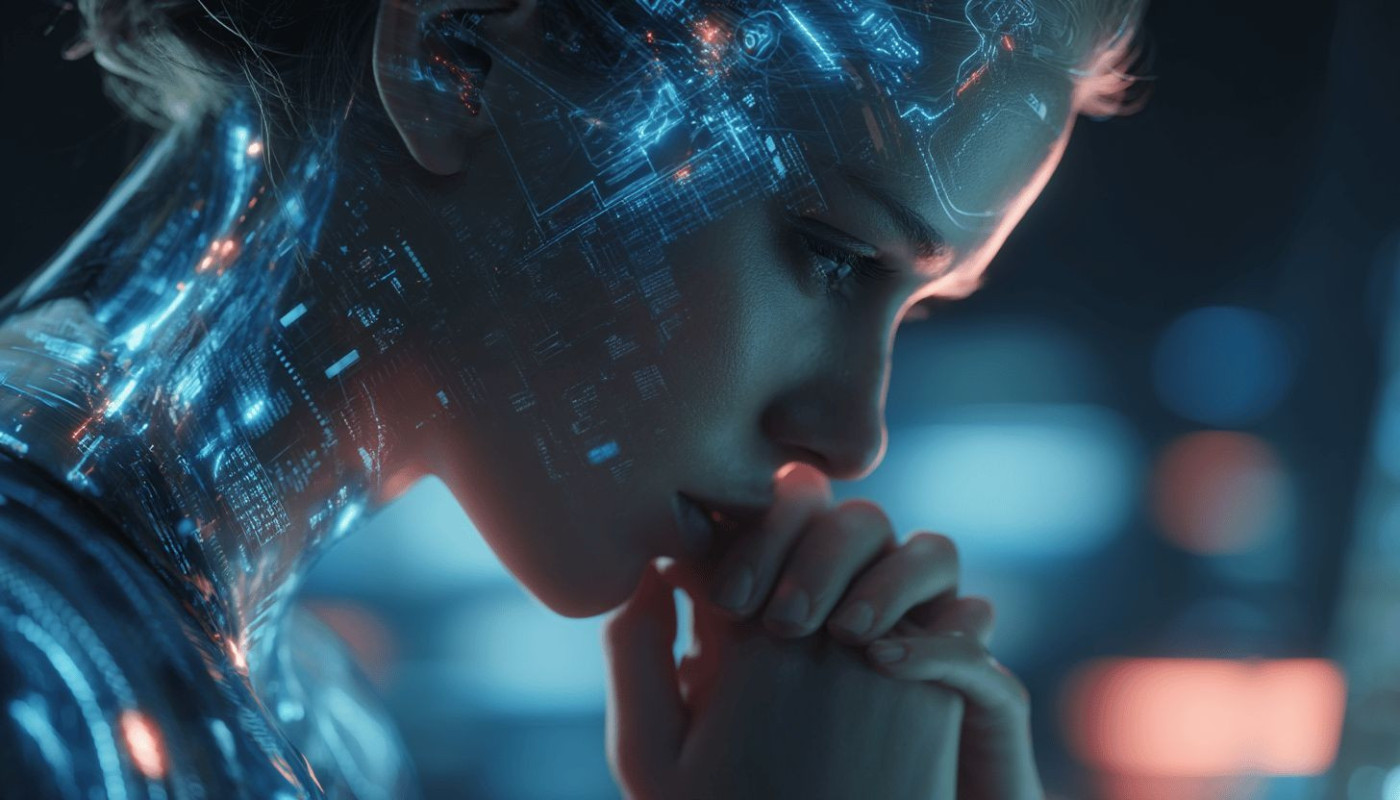
Maximiser l'efficacité professionnelle avec les technologies de modèles de langage
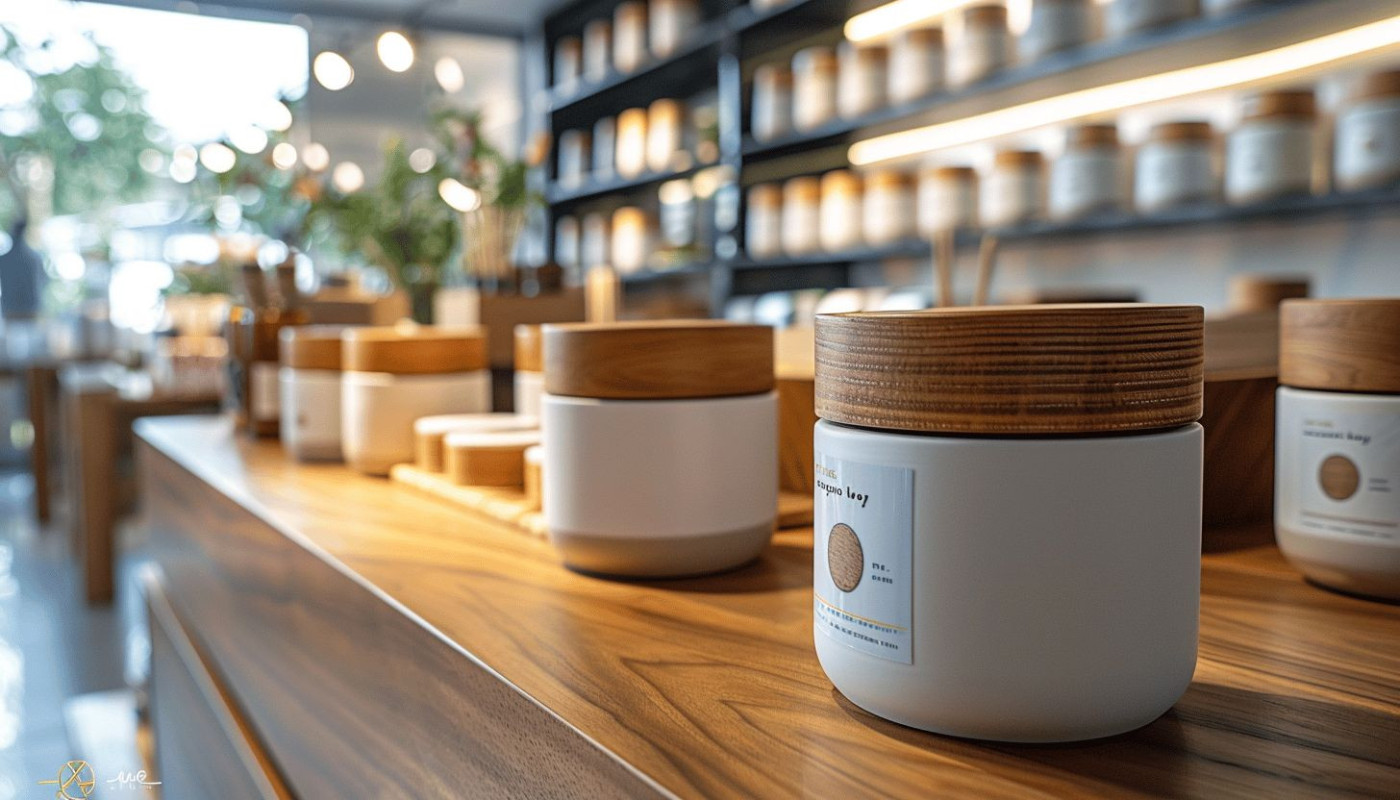
Création d'entreprise en niche conseils pour un lancement réussi
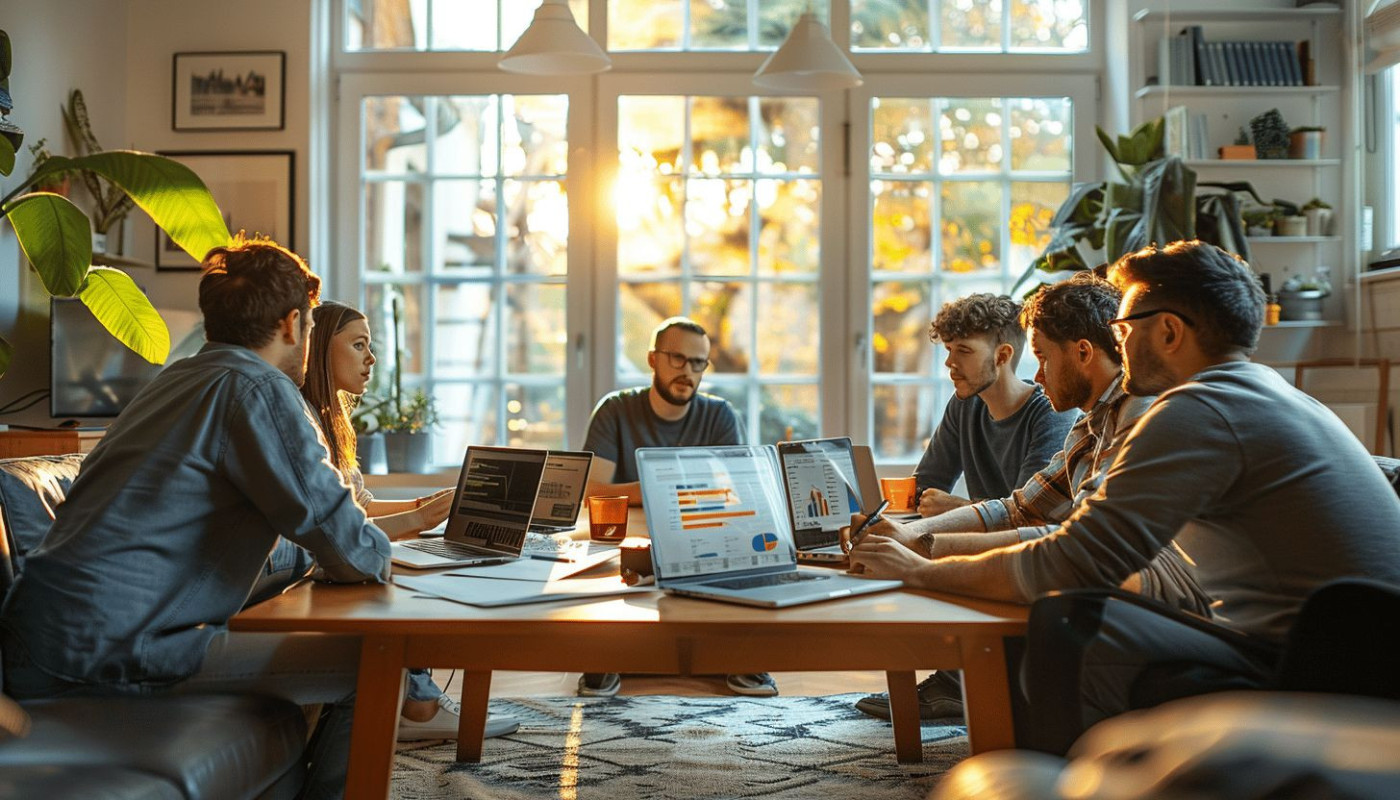
Financement participatif pour PME - planifier et lancer une campagne réussie
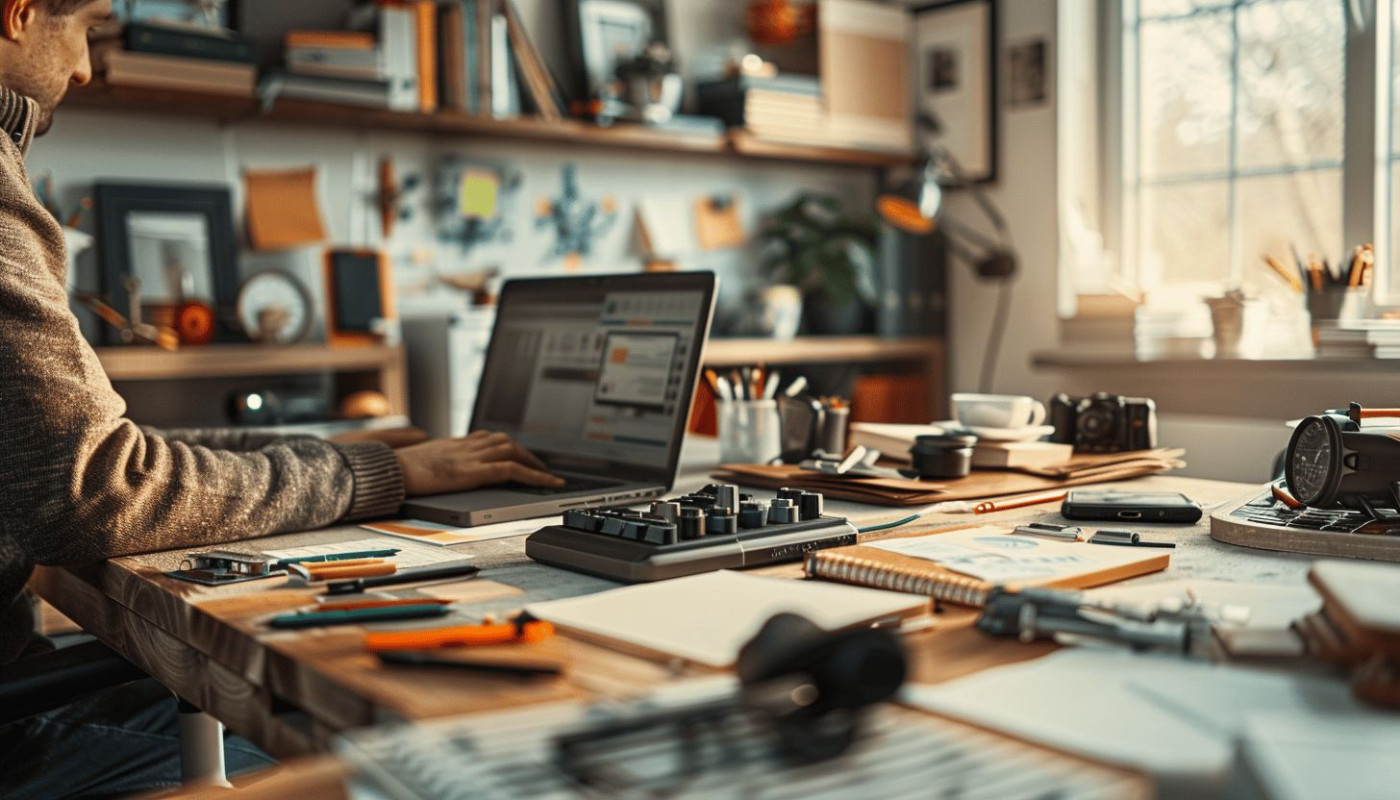
Télétravail et productivité outils et pratiques pour les entrepreneurs
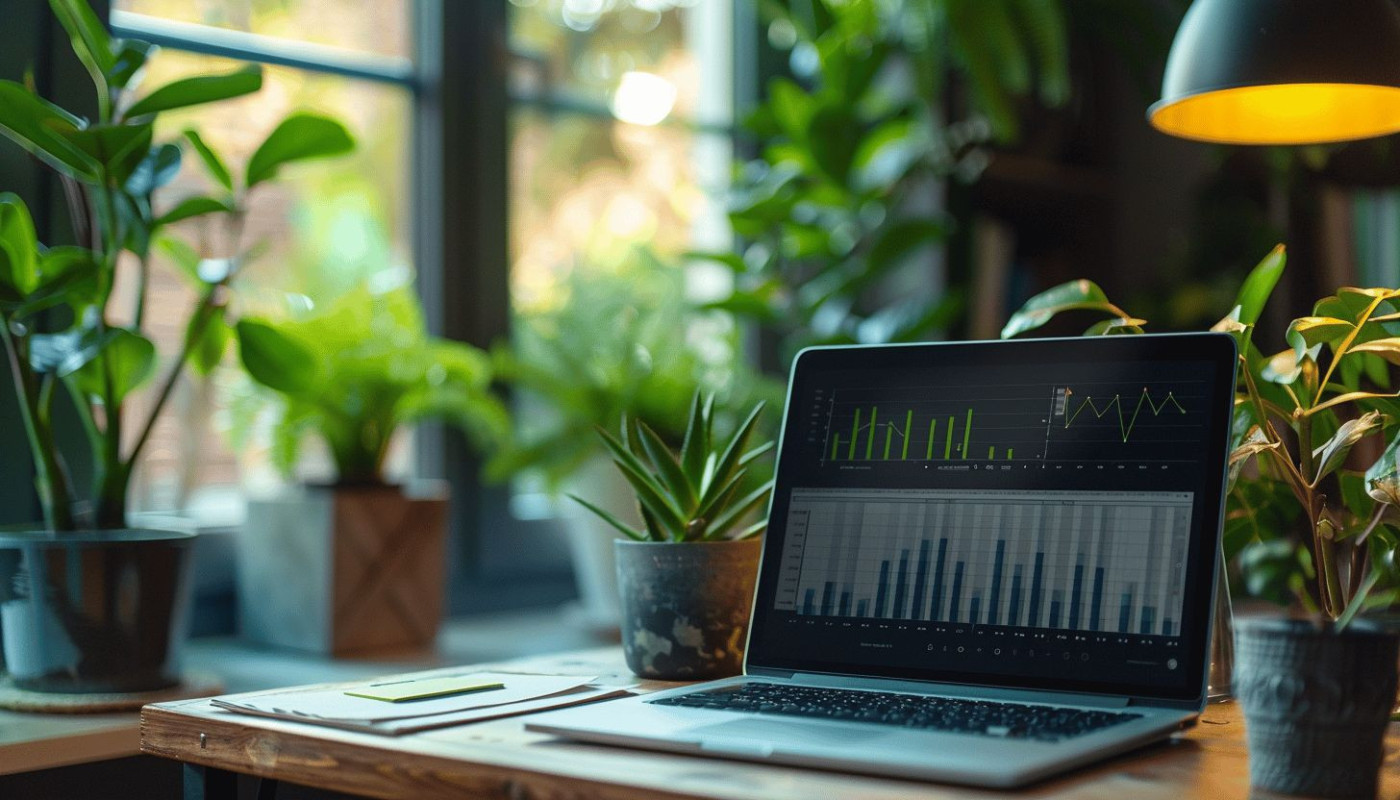
Les avantages de travailler avec une consultante SEO indépendante pour l'optimisation de site
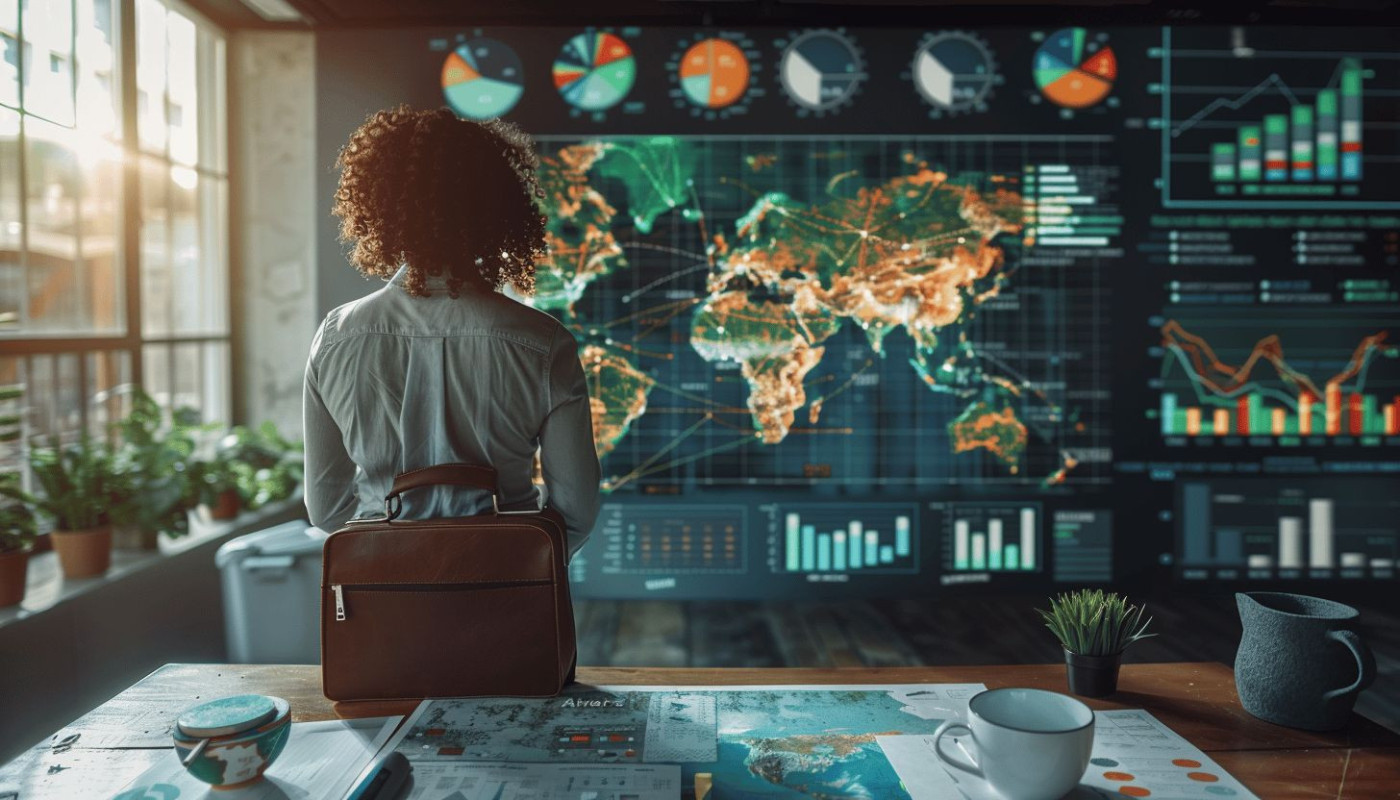
Les compétences clés pour réussir dans le commerce international

Impact des réformes de 2025 sur les parcours de formation professionnelle
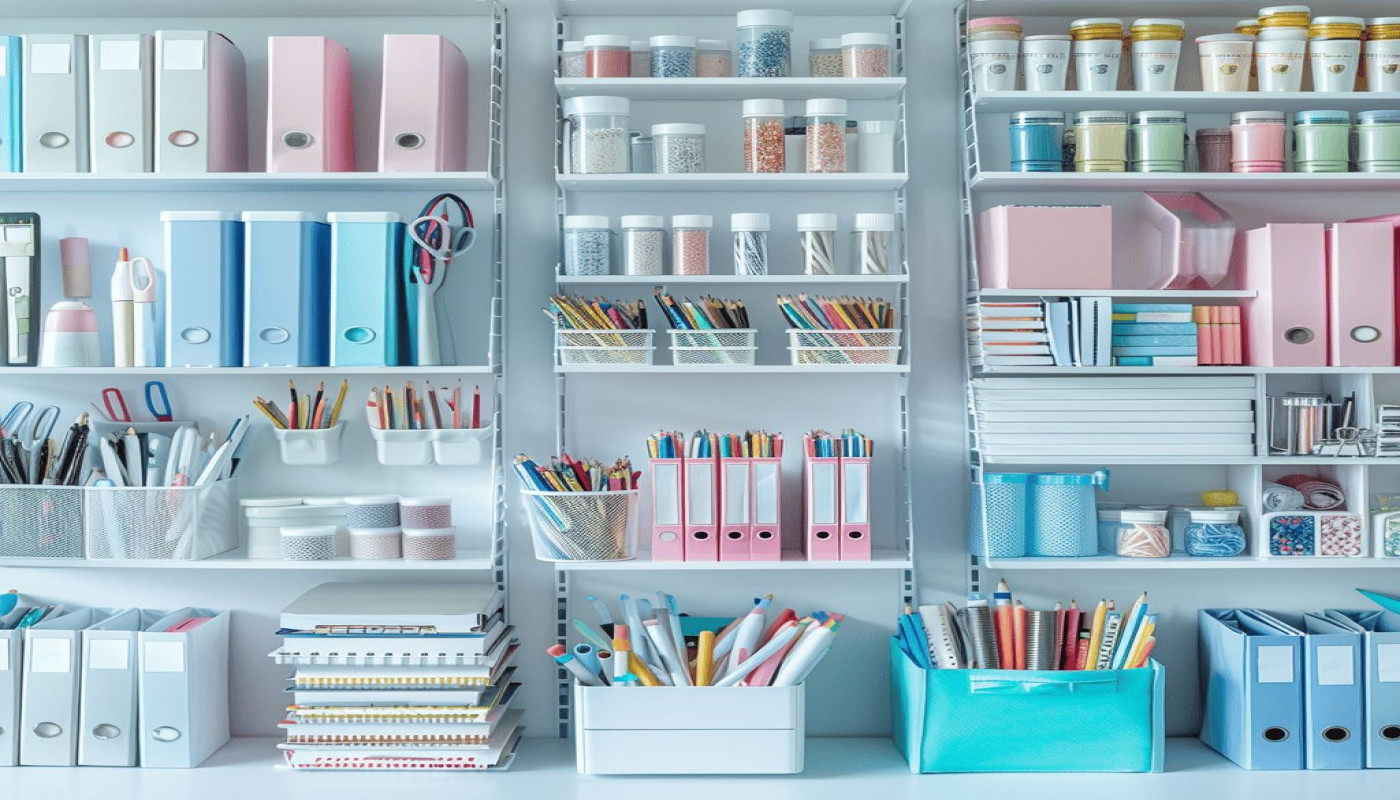
Comment choisir les fournitures de bureau essentielles pour une rentrée réussie
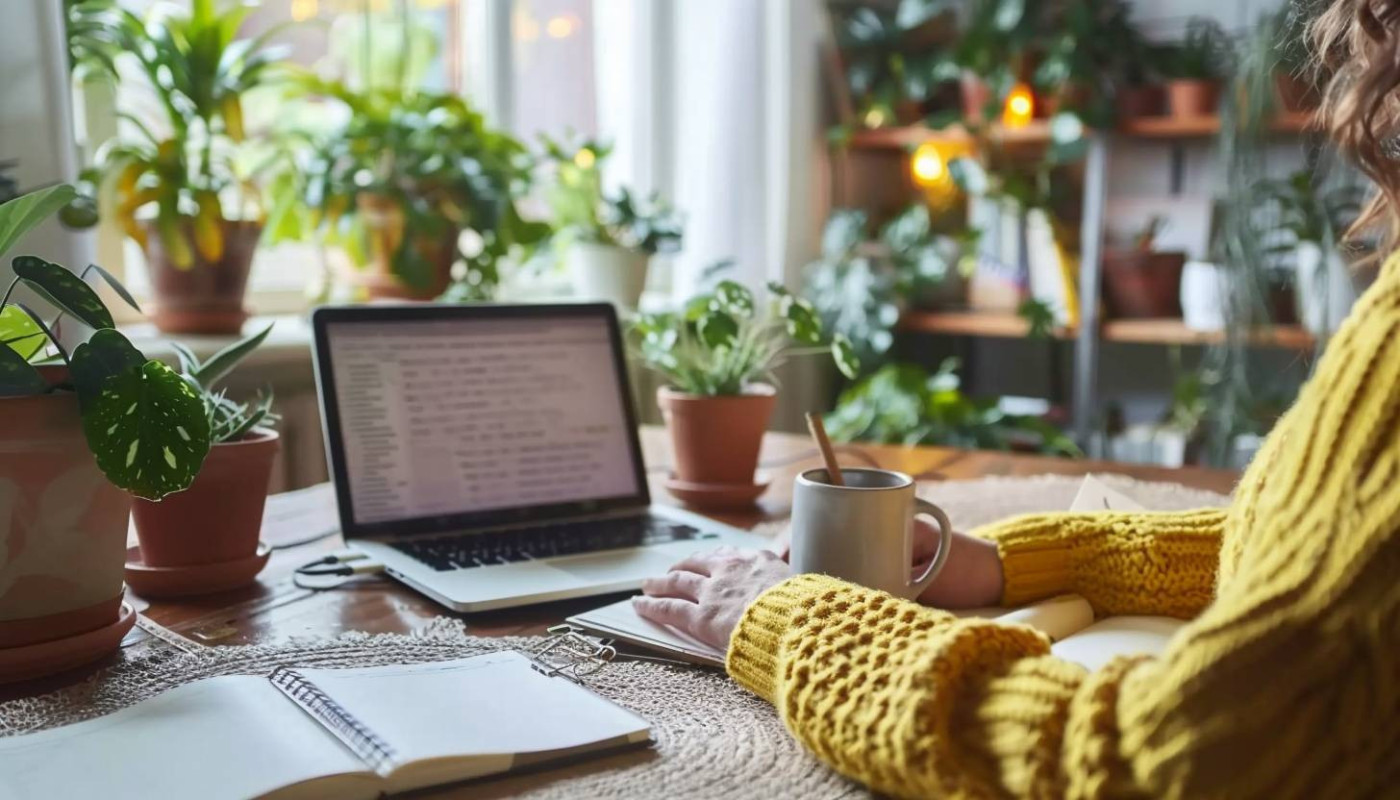
Stratégies efficaces pour une gestion optimale du télétravail
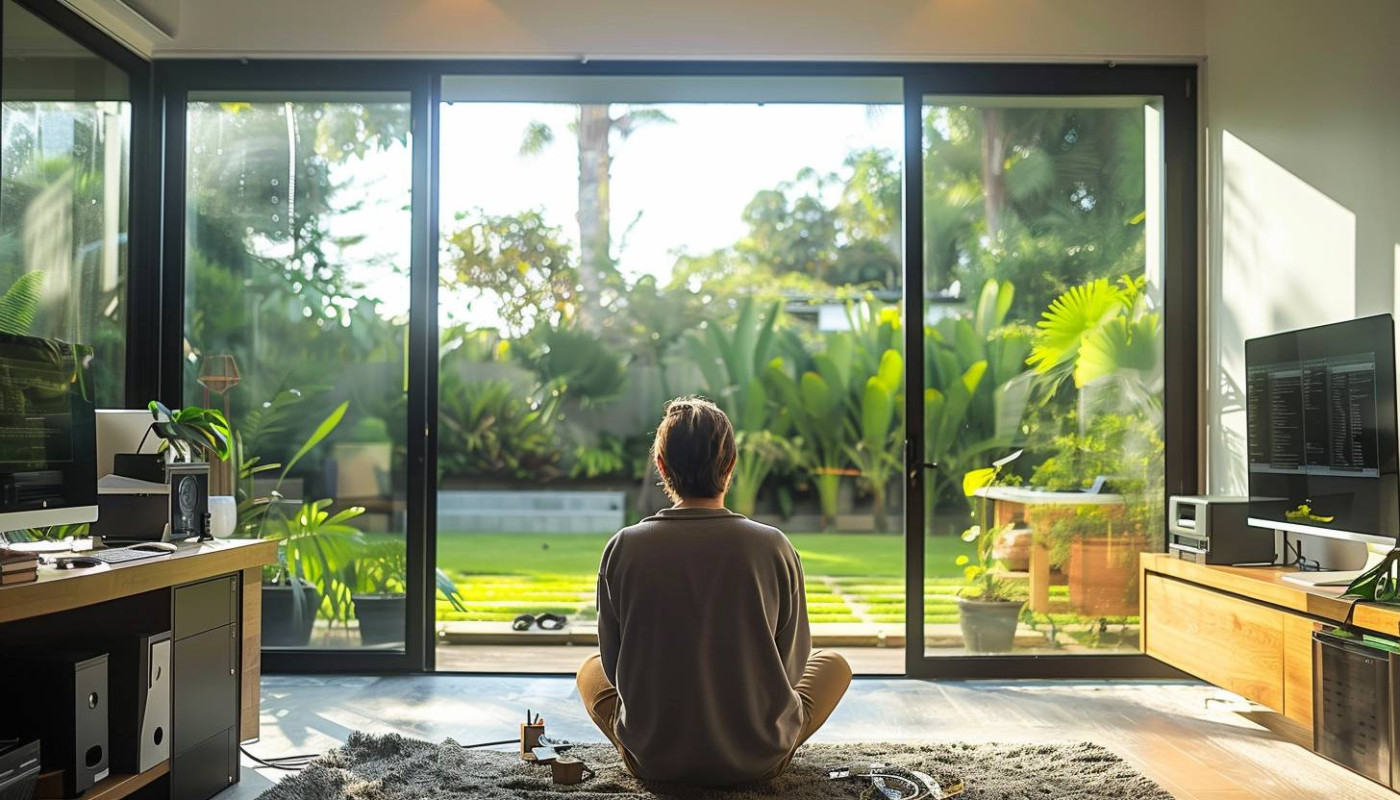
Stratégies pour maximiser l'efficacité du télétravail dans votre entreprise
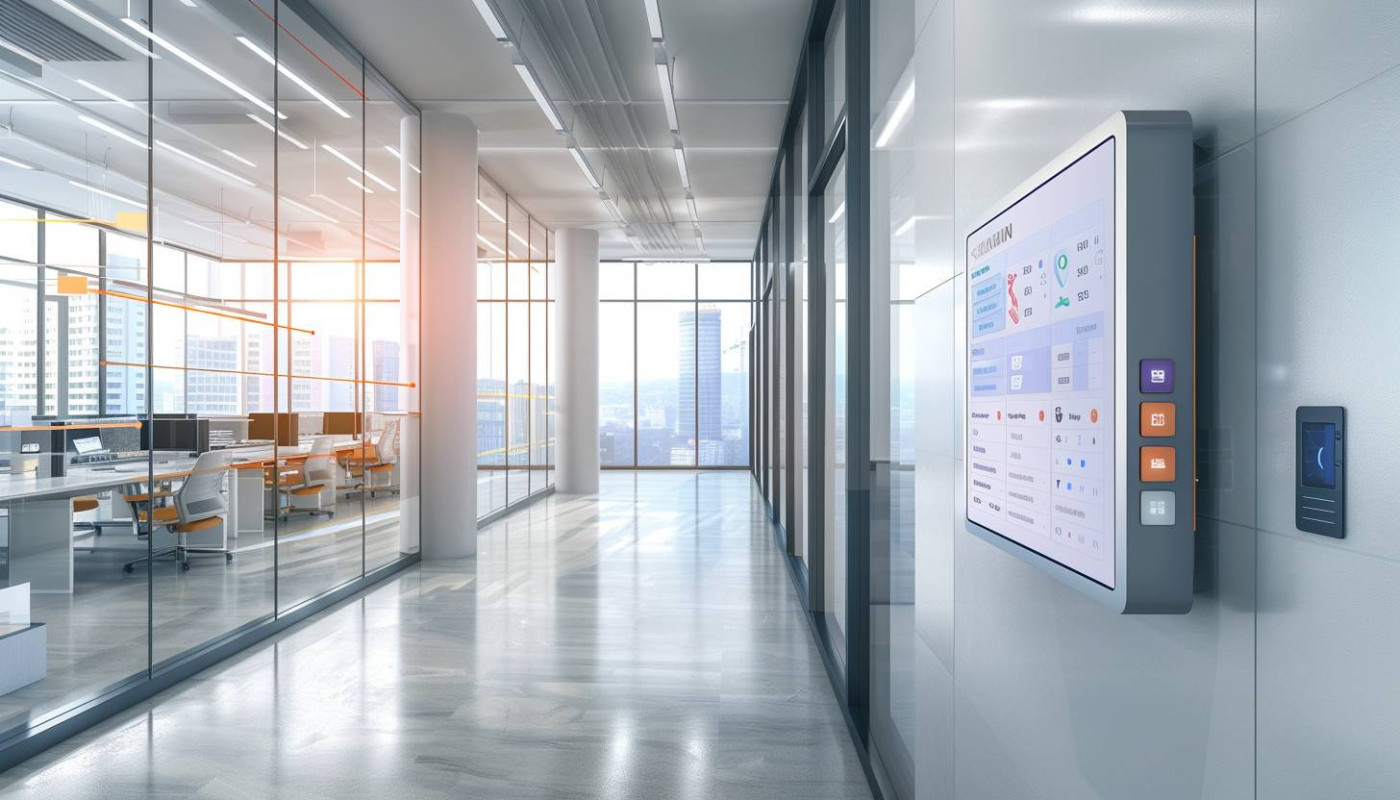
Comment un outil de gestion de la relation client peut transformer votre entreprise
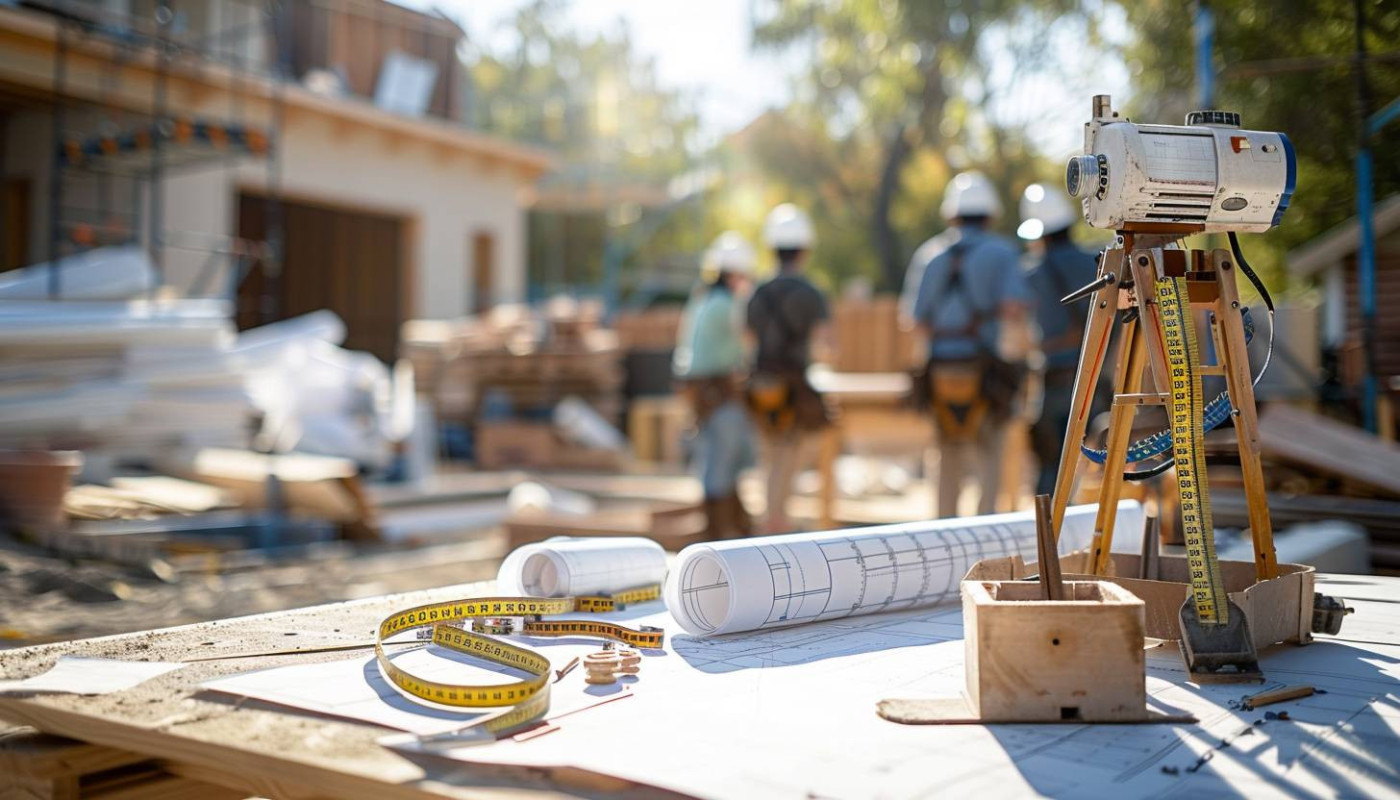
Les avantages des services de géométrie et topographie pour les projets de construction
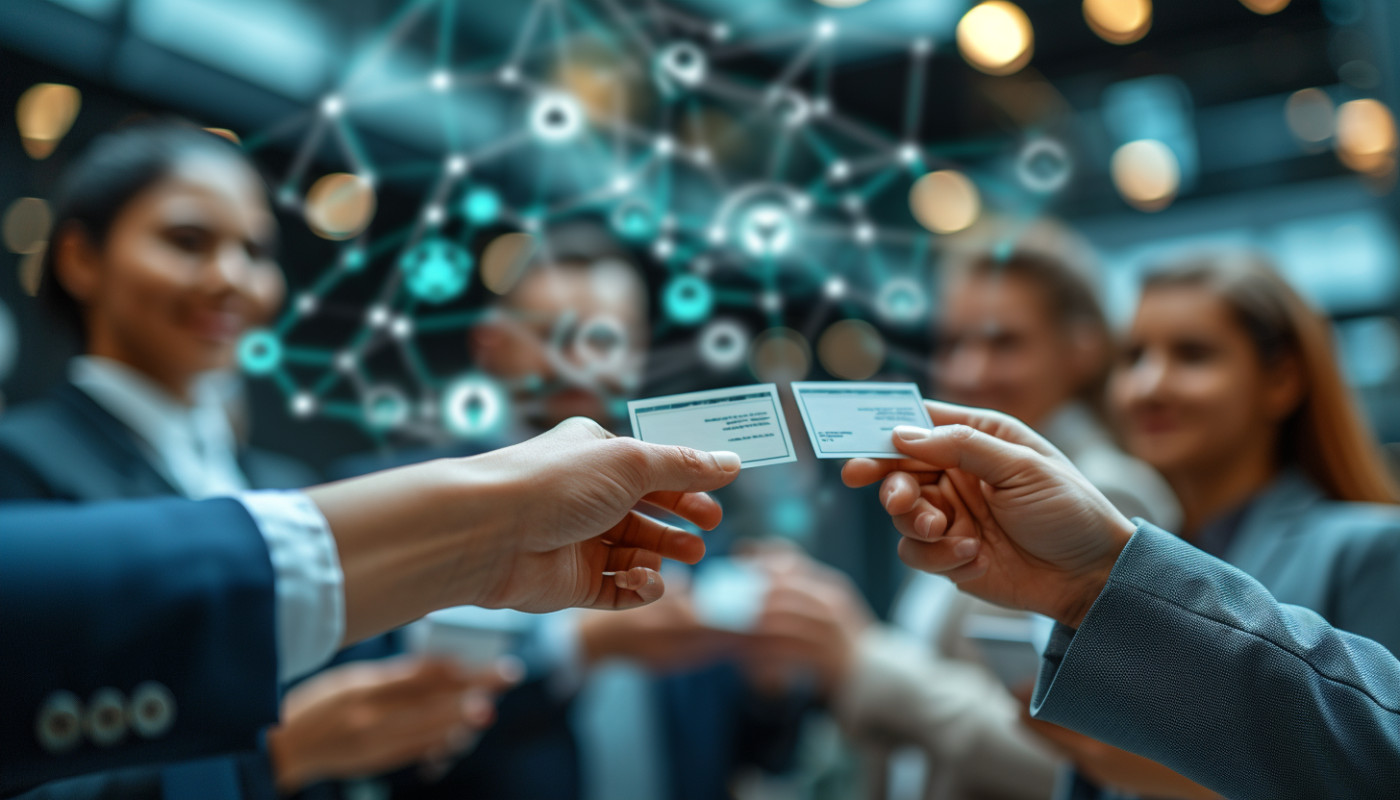
Comment les réseaux professionnels et les formations influencent la carrière dans le secteur des affaires
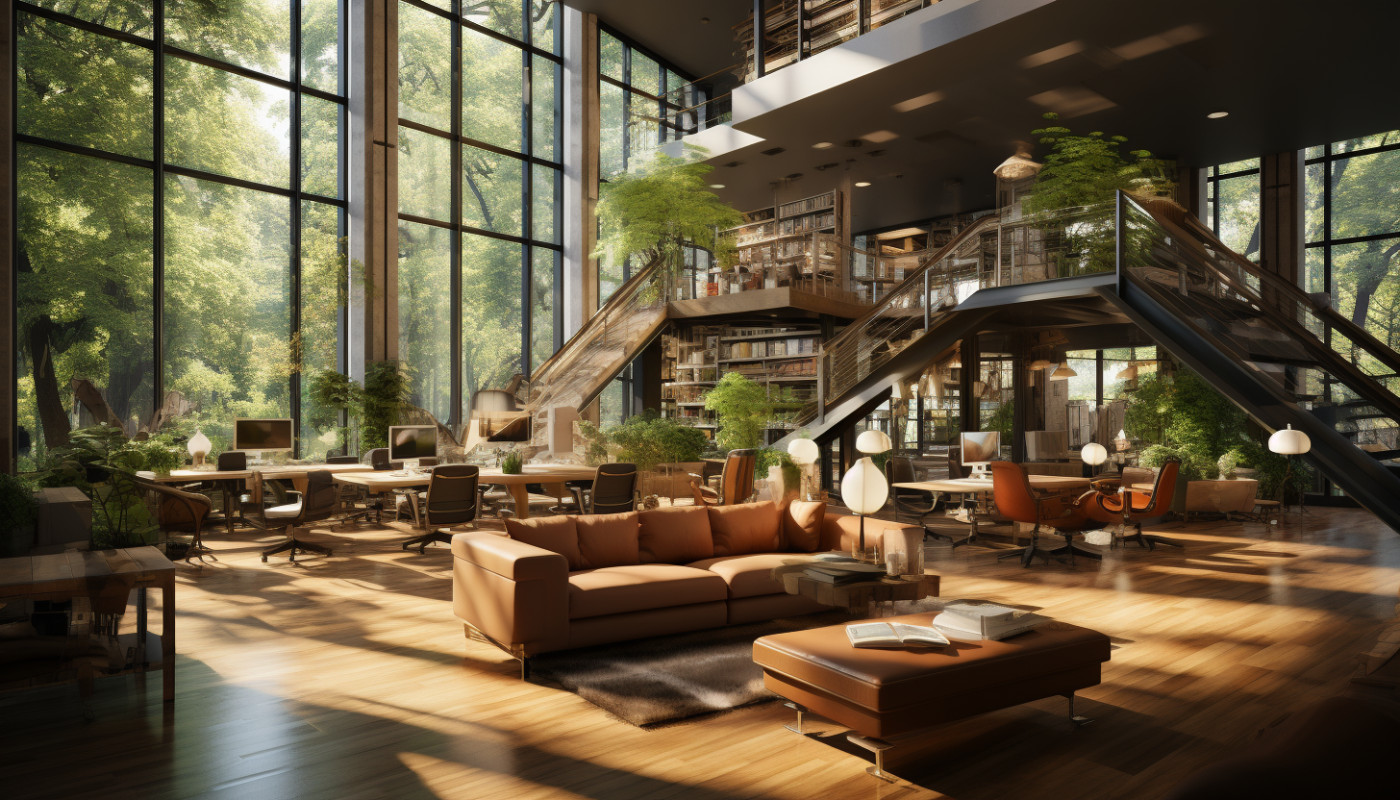
Comment le design de bureau influence-t-il la culture d'entreprise ?
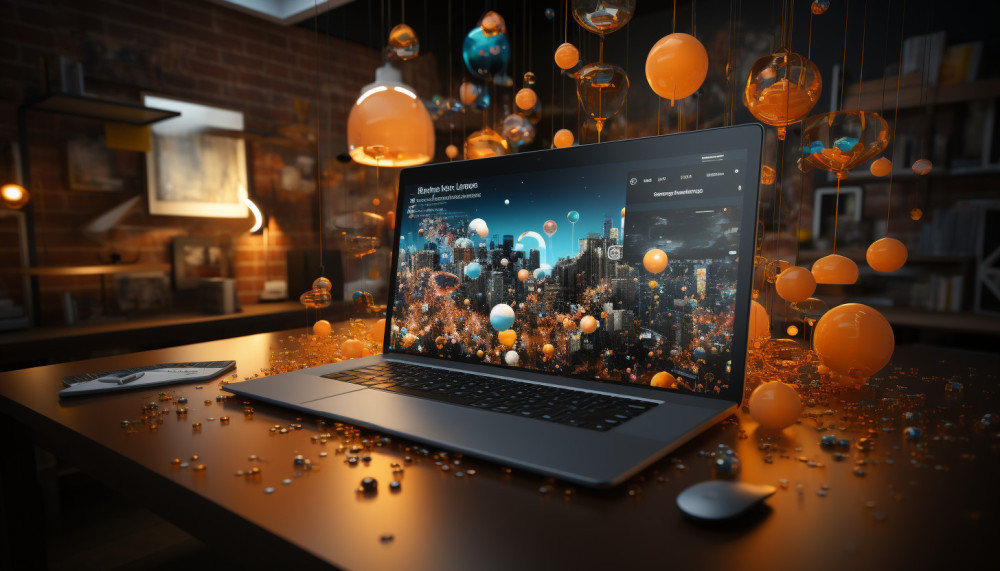
En quoi le marketing digital est-il indispensable pour la réussite d’un projet ?
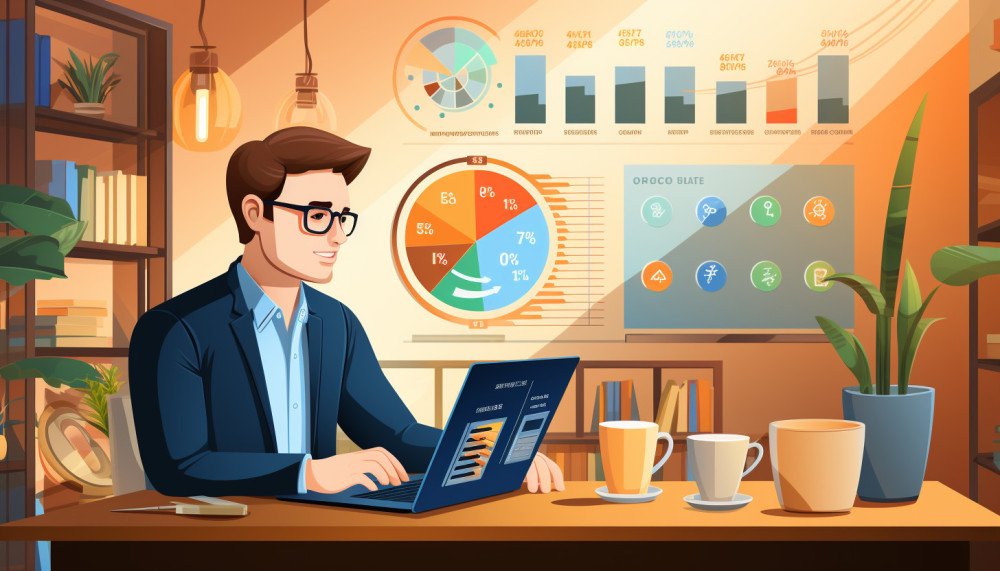
L'impact du télétravail sur la performance commerciale : analyse et perspectives
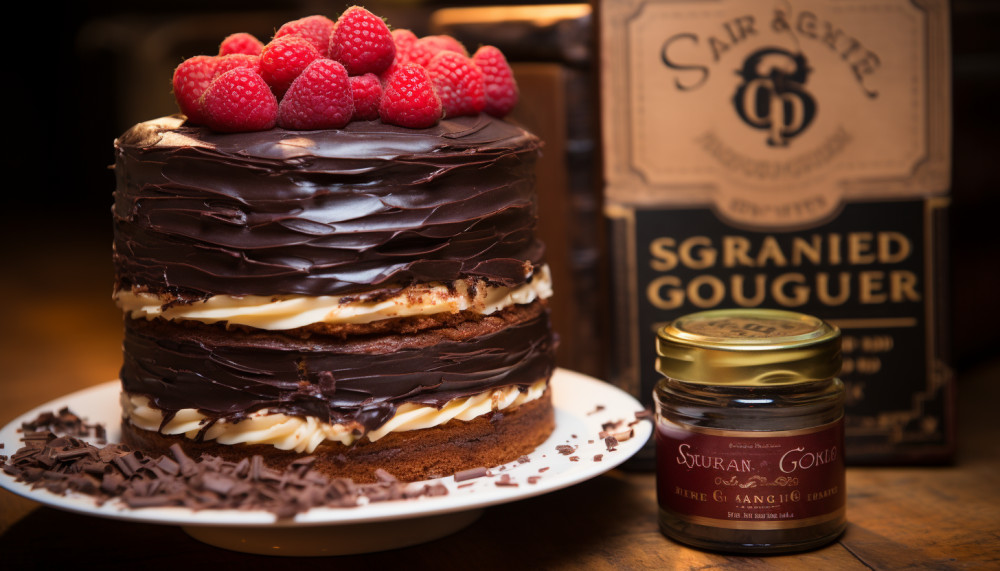